<!DOCTYPE html>
<html lang="en">
<head>
<meta charset="UTF-8">
<meta name="viewport" content="width=device-width, initial-scale=1.0">
<title>Handpan Tuning Article</title>
</head>
<body>
<article>
<p>The handpan, a captivating acoustic instrument noted for its ethereal resonance and unique design, has undergone profound transformations since its inception. The evolution of handpan tuning offers a compelling glimpse into the blend of tradition and innovation. From the rudimentary techniques employed by early makers to the sophisticated methods utilized by contemporary craftsmen, each phase reflects a growing understanding and appreciation for this remarkable instrument.</p>
<h2>Historical Background</h2>
<p>The journey of the handpan tuning process begins with the creation of the first steel pans in Trinidad in the early 20th century. These instruments emerged as a response to limitations placed on traditional drumming, giving birth to melodic percussion crafted from metal. As steelpan music gained popularity, so did the techniques for tuning these instruments to achieve accurate pitch and tone.</p>
<p>In 2000, Felix Rohner and Sabina Schärer of PANArt introduced the Hang, marking a significant evolution. The Hang was an amalgamation of traditional steelpan techniques and inspirations from instruments like the Ghatam and Udu, offering a new sound palette. The tuning technique was labor-intensive, involving precision hammering and careful tempering of the metal to achieve the desired note fields.</p>
<h2>Traditional Tuning Techniques</h2>
<p>In the early days, tuning a handpan was a meticulous process requiring skilled craftsmanship. This involved carefully heating and hammering steel sheets to create tuned notes. The steel's thickness, diameter, and degree of curvature were manipulated to determine the instrument's tonal quality. The use of hammers, both mechanical and manual, was essential to refine each note's pitch, sustain, and overtones.</p>
<p>Traditional tuners relied heavily on their auditory skills and experience. The process was more art than science, often passed down through mentorship and practice. Tuners listened intently to the harmonics produced in response to strikes and adjusted the tension and geometry of the pan surface accordingly. This method was time-consuming but produced handpans with rich, resonant soundscapes.</p>
<h2>The Transition to Scientific Methods</h2>
<p>As demand for handpans increased globally, craftsmen began exploring ways to improve the efficiency and accuracy of the tuning process. The introduction of digital tuners and acoustic analysis tools marked the beginning of a more scientific approach to handpan crafting. These innovations allowed tuners to visualize sound waves and overtones, providing an objective complement to their tuning skills.</p>
<p>Digital tuners offered precise measurements of frequency and amplitude, assisting tuners in achieving consistency across different instruments. Meanwhile, computer-aided designs (CAD) and 3D modeling influenced the manufacturing process, helping makers understand the impact of various shell geometries and materials on sound production.</p>
<h2>Innovations in Handpan Tuning</h2>
<p>Modern handpan tuning has seen the integration of cutting-edge technology, leading to instruments with unparalleled precision and versatility. The use of high-quality nitrided steel extended the longevity of the handpan's tuning stability by increasing resistance to environmental changes. This material innovation was crucial for enhancing the reliability and durability of handpans across diverse climates.</p>
<p>Automated tuning systems have also emerged, incorporating robotics and computer algorithms to refine the tuning process further. These systems allow for micro-adjustments, reducing the margin of error and enabling a higher degree of uniformity in sound character. By automating specific stages of the process, the craftsmanship is bolstered by technological precision.</p>
<p>Innovators in the handpan community have also experimented with alternate scales and innovative structural designs. The traditional diatonic and pentatonic scales have expanded into a myriad of exotic tunings, offering musicians a vast array of emotional and creative expressions. Experimentation with asymmetric and hybrid scales has led to new sonic frontiers that were previously unexplored.</p>
<h2>Balancing Artistry with Technology</h2>
<p>Despite these technological advancements, the art of handpan tuning remains deeply rooted in craftsmanship. Each tuner brings a unique touch informed by his or her understanding of acoustics and musicality. Balancing this artistry with technology ensures that each handpan has its own personality while maintaining the desired acoustic qualities.</p>
<p>Modern tuners strive to maintain the instrument's soulful and human connection. They appreciate that technology can enhance precision, yet the final tuning is often perfected through intuition, touch, and an intimate relationship with the instrument. Thus, the evolution of handpan tuning continues to reflect a fascinating blend of human artistry and scientific curiosity.</p>
<p>The future of handpan tuning looks promising as more advancements are likely to emerge, providing even finer control over acoustic variables. As makers push boundaries, the handpan's musical potential will continue to expand, offering a profound impact on both the creators and players of these beloved instruments.</p>
<h2>Conclusion</h2>
<p>Over the years, the art and science of handpan tuning have evolved considerably, beginning with traditional methods and culminating in the incorporation of modern technology. This evolution signifies a journey deeply intertwined with cultural expression and musical innovation. The interplay between ancient craftsmanship and contemporary advancements will continue to shape the identity and the acoustical brilliance of the handpan, ensuring it remains a vital instrument in the global music landscape. As makers and musicians from around the world contribute to its development, the future of handpan tuning stands on the brink of limitless possibilities, promising ever more captivating sonic journeys.</p>
<h2>Frequently Asked Questions</h2>
<dl>
<dt>Q1: How long does it take to tune a handpan?</dt>
<dd>A1: The time it takes to tune a handpan can vary depending on the experience of the tuner and the complexity of the desired scale. It typically ranges from a few hours to several days for fine-tuning.</dd>
<dt>Q2: What tools are used in the traditional handpan tuning process?</dt>
<dd>A2: Traditional handpan tuning involves the use of various hammers, both manual and mechanical, as well as tuning forks to assess pitch and overtones. Some craftsmen also use fire or heat to alter the metal's properties.</dd>
<dt>Q3: Can a handpan go out of tune?</dt>
<dd>A3: Yes, handpans can go out of tune due to environmental factors like temperature and humidity changes or physical impacts. High-quality nitrided steel pans are more resistant to these changes.</dd>
<dt>Q4: How is modern technology improving handpan tuning?</dt>
<dd>A4: Modern technology improves handpan tuning by incorporating precise digital tuners and automated systems for consistent note accuracy. Innovations in material and design also contribute to enhanced durability and tonal quality.</dd>
<dt>Q5: Do all handpans sound the same?</dt>
<dd>A5: No, each handpan has its unique sound profile influenced by its tuning scale, material, and craftsmanship. Variability in these factors leads to a wide diversity of soundscapes among handpans.</dd>
</dl>
</article>
</body>
</html>
The Evolution of Handpan Tuning: From Traditional Methods to Modern Innovations
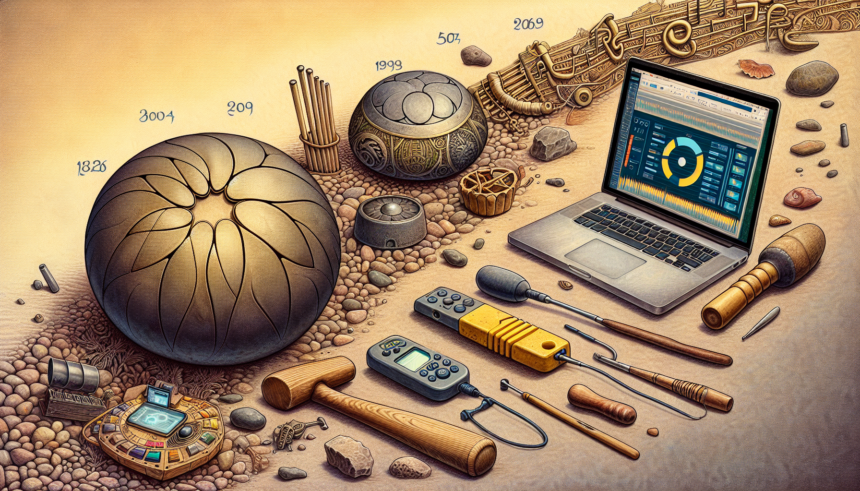
Leave a comment