<!DOCTYPE html>
<html lang="en">
<head>
<meta charset="UTF-8">
<meta name="viewport" content="width=device-width, initial-scale=1.0">
<title>The Craft of Handpan Tuning</title>
<style>
body {
font-family: Arial, sans-serif;
line-height: 1.6;
margin: 20px;
padding: 0;
background-color: #f4f4f9;
color: #333;
}
h2, h3 {
color: #2c3e50;
}
.faq {
background-color: #ecf0f1;
padding: 10px;
border-radius: 5px;
margin-top: 20px;
}
</style>
</head>
<body>
<section>
<h2>Introduction</h2>
<p>
The handpan, an enticing percussion instrument known for its ethereal sounds, captures the imagination of many musicians worldwide. Its unique, resonant tones result from a meticulous process known as handpan tuning. This art requires considerable skill and precision, as the handpan is essentially a melodic drum that needs to be perfectly tuned to deliver its characteristic sound. In this article, we will explore the skills, tools, and techniques involved in the craft of handpan tuning.
</p>
</section>
<section>
<h2>The Skills of Handpan Tuning</h2>
<p>
Handpan tuning is not just about hitting a piece of metal; it is a skill that combines the art and science of sound engineering. A handpan tuner must possess a keen ear for music and a profound understanding of acoustics. The ability to distinguish subtle differences in pitch and tone is crucial. Additionally, the tuner must appreciate the interplay between the handpan's physical structure and its acoustic properties.
</p>
<p>
Experience is another essential skill. Master tuners typically spend years honing their craft, learning from trial and error before successfully tuning a handpan to its optimal sound. Patience and precision are critical traits, as even a minor error can result in an instrument that doesn't sing properly.
</p>
</section>
<section>
<h2>Tools of the Trade</h2>
<p>
Handpan tuning requires a specific set of tools that help the tuner manipulate and shape the metal to achieve desired tonal qualities. One of the primary tools is a set of hammers of various sizes and weights. These hammers are used to carefully adjust the tension and curvature of the steel to modify its pitch.
</p>
<p>
Another essential tool is the strobe tuner, a highly accurate device that helps in precisely measuring the handpan’s pitch. This device provides visual confirmation of the tuner’s auditory perceptions, ensuring that the notes are perfectly aligned according to the desired scale.
</p>
<p>
Additionally, specialized anvils or forms are used to support the handpan during the tuning process, allowing for precise adjustments without damaging the instrument.
</p>
</section>
<section>
<h2>Techniques of Handpan Tuning</h2>
<p>
The handpan tuning process involves several intricate techniques that each serve crucial functions in shaping the instrument's sound. Firstly, the initial shaping of the handpan's shell is akin to sculpting, as it involves molding the raw steel into a dome-like form that can resonate effectively.
</p>
<p>
Following the shaping, the rough tuning phase begins. This involves establishing the basic pitches of the handpan by striking the dimples on the surface with tuning hammers. The objective is to bring the instrument close to the desired scale, but not necessarily to perfect pitch.
</p>
<p>
The fine-tuning process is where the skill of the tuner truly shines. During this stage, the tuner makes precise adjustments to refine each note to the exact frequency needed. This involves delicate hammer strikes and may require retuning multiple times to achieve the perfect resonance and timbre.
</p>
<p>
Finally, stabilizing the tuning ensures the handpan maintains its pitch over time. Heat treatments and specific surface finishes may be applied to enhance the instrument's durability and reduce susceptibility to environmental factors such as humidity or temperature changes.
</p>
</section>
<section>
<h2>Conclusion</h2>
<p>
The craft of handpan tuning is a sophisticated blend of art, science, and skill. A successful handpan tuner possesses a deep musical intuition, technical prowess, and meticulous attention to detail. Their tools and techniques are refined over years, guided by an innate understanding of acoustics and metalworking. While handpan tuning is undeniably complex, its outcome — the creation of a harmonious, resonant instrument — is a testament to the tuner’s dedication and craftsmanship. As interest in handpans grows, so does the appreciation for the tuners who transform raw metal into melodic art.
</p>
</section>
<section class="faq">
<h3>FAQs</h3>
<h4>Q1: How long does it take to learn handpan tuning?</h4>
<p>
A1: Learning handpan tuning can take several years of practice. Becoming proficient typically involves understanding acoustic principles, practicing metalworking skills, and developing a refined ear for music.
</p>
<h4>Q2: What materials are handpans made from?</h4>
<p>
A2: Handpans are generally made from steel, with some manufacturers using special alloys or nitrided steel to enhance durability and acoustic properties.
</p>
<h4>Q3: Can handpans go out of tune?</h4>
<p>
A3: Yes, handpans can go out of tune due to environmental factors like humidity and temperature changes or physical impacts. Regular tuning maintenance can help keep them in prime condition.
</p>
<h4>Q4: Is electronic tuning possible for handpans?</h4>
<p>
A4: While there are electronic tuning aids and software that can assist in the tuning process, handpans are primarily tuned manually by skilled tuners using acoustic techniques.
</p>
<h4>Q5: How often should a handpan be tuned?</h4>
<p>
A5: The frequency of tuning depends on how frequently the handpan is played and the conditions in which it’s stored. Typically, a handpan might need retuning every few years or as soon as noticeable detuning occurs.
</p>
</section>
</body>
</html>
The Craft of Handpan Tuning: Skills, Tools, and Techniques
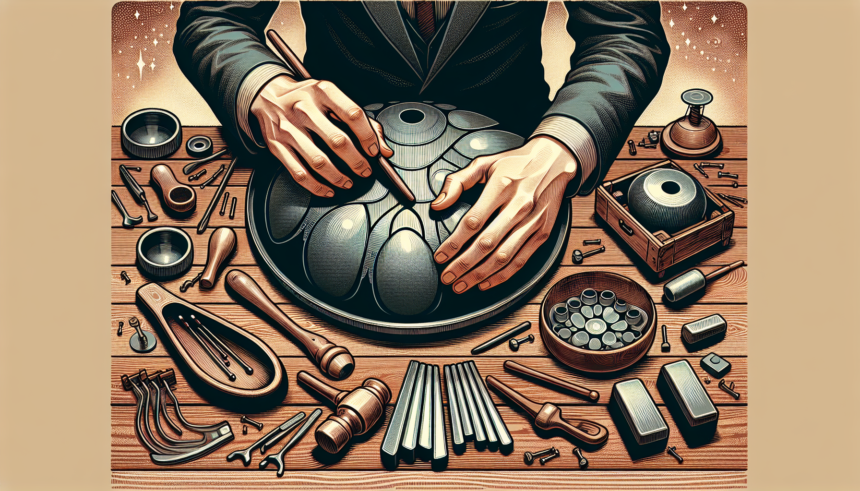
Leave a comment