<!DOCTYPE html>
<html lang="en">
<head>
<meta charset="UTF-8">
<meta name="viewport" content="width=device-width, initial-scale=1.0">
<title>The Evolution of Handpan Craftsmanship</title>
<style>
body {
font-family: Arial, sans-serif;
line-height: 1.6;
margin: 20px;
}
h1, h2, h3 {
color: #333;
}
ul {
margin-left: 20px;
}
</style>
</head>
<body>
<h1>From Steel to Melody: The Evolution of Handpan Craftsmanship</h1>
<p>The handpan, a relatively new addition to the world of musical instruments, has captured the imaginations of musicians and listeners alike with its ethereal soundscapes and unique, resonant tones. The journey from raw steel to the intricate handpan is one characterized by a blend of ancient techniques, modern innovations, and a deep understanding of acoustics and craftsmanship. This article delves into the evolution of handpan craftsmanship, exploring its origins, development, and the future of this mesmerizing instrument.</p>
<h2>Origins of the Handpan</h2>
<p>The handpan, also known as the hang drum or simply hang, was first created in the early 2000s by Swiss musicians Felix Rohner and Sabina Schärer of PANArt. Inspired by the steel drum, an instrument native to Trinidad and Tobago, they sought to create an instrument with a similar percussive quality but with more tonal variety and melodic possibilities. The result was the hang, a name derived from the Bernese German word for "hand".</p>
<p>The hang consists of two half-shells of nitrided steel, formed into a convex shape and adhered together at the rim. The top shell, known as the "ding side", features a central dome and several tone fields around it, each corresponding to a specific note. The bottom shell, or "gu side", often includes a resonant hole. The instrument is played with the hands, creating a wide range of dynamics and expressive possibilities.</p>
<h2>Craftsmanship Techniques</h2>
<h3>Nitriding the Steel</h3>
<p>The process of creating a handpan begins with the preparation of the steel itself. Nitriding, a form of case hardening, is a critical step. This involves introducing nitrogen into the steel's surface to increase its hardness and resistance to wear. This treatment is essential for producing the characteristic sustain and resonance of the handpan, as the hardened surface can better support the instrument's vibrant, ringing tones.</p>
<h3>Shaping the Shells</h3>
<p>After nitriding, the steel is then shaped into the familiar domed shells. Traditionally, this is done by hand-hammering, a labor-intensive process that requires great skill and precision. Modern handpan makers might also employ hydraulic presses to achieve the initial shape before refining it by hand. The ultimate goal is to create a consistent thickness and curvature that will enhance both the structural integrity and acoustic properties of the instrument.</p>
<h3>Creating the Tone Fields</h3>
<p>One of the most crucial aspects of handpan craftsmanship is the creation of the tone fields. These are carefully placed and sculpted areas on the ding side of the shell that produce specific notes when struck. Each tone field must be meticulously shaped and fine-tuned to ensure accurate pitch and harmonious overtones. This involves a combination of techniques, including precise hammering, shaping, and tempering.</p>
<h3>Tuning the Handpan</h3>
<p>Tuning a handpan is a highly specialized process that requires a deep understanding of acoustics. Each tone field needs to be individually tuned to resonate at a specific frequency, often involving multiple tuning sessions to achieve the desired sound. Makers use a combination of electronic tuning devices and their trained ears to fine-tune each note, ensuring that the resulting instrument has a clear, balanced, and harmonic soundscape.</p>
<h2>Innovations in Handpan Craftsmanship</h2>
<p>Since the creation of the original hang, numerous innovations have emerged in the world of handpan craftsmanship. These developments have expanded the possibilities for both makers and musicians, leading to a diverse array of handpans with varying tonal qualities and characteristics.</p>
<h3>Material Variety</h3>
<p>While nitrided steel remains a popular choice, makers have experimented with other materials, such as stainless steel and even titanium. Each material offers unique acoustic properties and presents different challenges for shaping and tuning. For instance, stainless steel is known for its bright, clear tones, while titanium produces a warmer, more mellow sound. These material variations allow for a broader spectrum of sonic possibilities and cater to individual preferences.</p>
<h3>Hybrid Techniques</h3>
<p>Contemporary handpan makers often blend traditional handcrafting techniques with modern technologies. For example, computer-aided design (CAD) software can be used to model and simulate the acoustic properties of different shell shapes and tone field placements. This allows makers to experiment and refine their designs before committing to the labor-intensive process of shaping and tuning the actual instrument. Additionally, some makers utilize laser cutting and CNC (computer numerical control) machining to achieve greater precision in their work.</p>
<h3>Customizable Options</h3>
<p>One of the exciting developments in handpan craftsmanship is the ability to customize instruments to suit individual preferences. Makers can create handpans with specific scales, tunings, and even artwork. Some musicians prefer certain scales for particular genres or playing styles, and makers accommodate these preferences by crafting handpans that meet their unique requirements. This level of customization fosters a deeper connection between the musician and their instrument.</p>
<h2>The Future of Handpan Craftsmanship</h2>
<p>The art of handpan craftsmanship continues to evolve, driven by a growing community of makers, musicians, and enthusiasts. As the popularity of handpans spreads worldwide, so too does the innovation and exploration within the craft.</p>
<h3>Collaborative Efforts</h3>
<p>Collaboration among makers and musicians is a key factor in the ongoing development of handpan craftsmanship. Workshops, festivals, and online communities provide platforms for exchanging ideas, techniques, and insights. This collaborative spirit fosters a sense of camaraderie and shared purpose, pushing the boundaries of what is possible with the instrument.</p>
<h3>Sustainability and Ethical Practices</h3>
<p>As the demand for handpans grows, there is an increasing focus on sustainability and ethical practices within the craft. Makers are exploring ways to source materials responsibly and minimize their environmental impact. Additionally, some makers are committed to fair labor practices and ensuring that their instruments are accessible to a wider audience, rather than catering exclusively to premium markets.</p>
<h3>Educational Initiatives</h3>
<p>Educational initiatives are also playing a significant role in the future of handpan craftsmanship. Many experienced makers offer workshops and apprenticeships to pass on their knowledge and skills to the next generation. This transfer of expertise ensures that the art of handpan making continues to thrive and evolve, preserving the traditions while embracing new innovations.</p>
<h2>Conclusion</h2>
<p>The evolution of handpan craftsmanship is a testament to the harmonious blend of tradition and innovation. From its origins as a novel creation inspired by the steel drum to its current status as a beloved instrument with a dedicated following, the handpan's journey is one of relentless exploration and refinement. Through a combination of ancient techniques and modern advancements, makers have transformed raw steel into instruments of profound beauty and resonance. As the craft continues to develop, it promises to deliver even more captivating melodies and enrich the musical landscape for generations to come.</p>
<h2>FAQs</h2>
<h3>1. What is the difference between a handpan and a hang drum?</h3>
<p>The term "hang drum" is often used interchangeably with "handpan," but they originate from different contexts. The "hang drum" specifically refers to the instrument created by PANArt in the early 2000s. "Handpan" is a more general term that encompasses a variety of similar instruments developed by different makers since the introduction of the original hang.</p>
<h3>2. How long does it take to make a handpan?</h3>
<p>The time required to make a handpan can vary significantly depending on the maker's experience and the complexity of the instrument. On average, it can take several weeks to months to complete a single handpan, as the process involves meticulous shaping, tuning, and refining of both the shell and the tone fields.</p>
<h3>3. Can handpans be retuned?</h3>
<p>Yes, handpans can be retuned, but it is a delicate and specialized process that should be performed by an experienced maker. Over time, handpans may lose their tuning due to factors like environmental changes or frequent playing. A professional retuning can restore the instrument's original sound quality.</p>
<h3>4. What scales are available for handpans?</h3>
<p>Handpans are available in a wide range of scales, each with its own distinct mood and character. Common scales include D Minor, Celtic Minor, Integral, and Pygmy. Many makers also offer customizable scales to suit the specific preferences of individual musicians.</p>
<h3>5. How should I care for my handpan?</h3>
<p>Proper care is essential to maintain the longevity and sound quality of your handpan. It is important to keep the instrument clean and dry, and to store it in a protective case when not in use. Regularly applying a thin layer of oil to the surface can help prevent rust and corrosion. Avoid exposing the handpan to extreme temperatures or moisture, as these conditions can adversely affect the instrument.</p>
</body>
</html>
From Steel to Melody: The Evolution of Handpan Craftsmanship
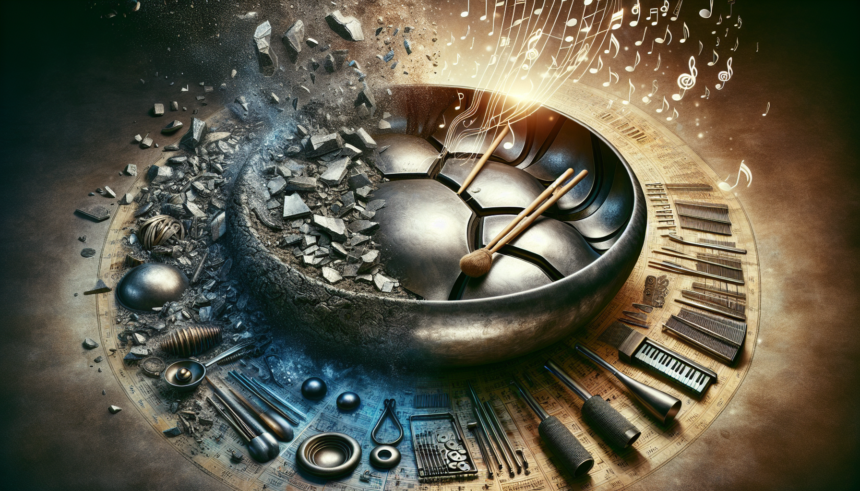
Leave a comment