<!DOCTYPE html>
<html lang="en">
<head>
<meta charset="UTF-8">
<meta name="viewport" content="width=device-width, initial-scale=1.0">
<title>Sound Sculpture: Innovative Techniques in Handpan Manufacturing</title>
<style>
body {
font-family: Arial, sans-serif;
line-height: 1.6;
margin: 0;
padding: 0;
}
header {
background: #333;
color: #fff;
padding: 10px 0;
text-align: center;
}
.container {
padding: 20px;
}
h1 {
color: #333;
text-align: center;
}
h2 {
color: #555;
}
ul {
margin: 20px 0;
padding: 0;
}
li {
list-style-type: none;
}
.faq-section {
margin-top: 40px;
background: #f4f4f4;
padding: 20px;
border-radius: 8px;
}
</style>
</head>
<body>
<header>
<h1>Sound Sculpture: Innovative Techniques in Handpan Manufacturing</h1>
</header>
<div class="container">
<p>The sound sculpture, specifically the handpan, is a mesmerizing instrument that resonates with celestial tones, capturing the imagination of musicians and listeners alike. Originating in the early 2000s, the handpan is a unique musical tool that owes its enchanting sounds to intricate craftsmanship and innovative manufacturing techniques.</p>
<h2>History and Evolution</h2>
<p>The handpan's journey began with the introduction of the Hang by PANArt in Switzerland in 2000. The Hang, influenced by earlier Caribbean steelpan designs and tuned idiophones, set the stage for the modern handpan. As the instrument's popularity surged, various artisans ventured into creating their versions, ultimately evolving the craftsmanship and techniques used in handpan manufacturing.</p>
<p>Handpan makers, often referred to as 'pan builders' or 'tuner artisans', have continuously experimented with materials and methods to achieve distinct sounds and durability. Over the years, innovations have led to significant advancements in how these instruments are crafted.</p>
<h2>Material Selection</h2>
<p>The choice of material is fundamental in handpan manufacturing. Initially, makers predominantly used nitrided steel, which offered corrosion resistance and durability while providing a stable, resonant sound. Today, many builders have moved towards using stainless steel, owing to its superior rust resistance and a unique, brighter tone.</p>
<p>However, the shift towards stainless steel isn't merely about rust resistance. It also offers a different aesthetic appeal and acoustic properties. The choice between nitrided and stainless steel often boils down to the specific tonal qualities a maker aims to achieve. Some manufacturers even explore hybrid materials, combining different metals to find the perfect balance between sound and longevity.</p>
<h2>Shaping and Forming</h2>
<p>One of the critical steps in handpan manufacturing is shaping the steel into a dome. Traditionally, this was done manually with hammers, requiring immense skill and precision. Today, hydraulic presses and spinning techniques offer more consistent and controlled shaping, significantly reducing the labor-intensive nature of the process.</p>
<p>Despite advancements, many artisans still prefer hand-hammering for the unique character it imparts to each instrument. It allows for fine-tuning the tension and thickness of the steel, which directly impacts the instrument's sound quality. The balance between traditional hand techniques and modern machinery often defines the distinct sound and feel of a handpan.</p>
<h2>Tuning and Acoustic Perfection</h2>
<p>Tuning a handpan is akin to sculpting sound itself. After shaping, the next step involves meticulously tuning the instrument. This process is both an art and a science, requiring an acute ear and sophisticated tools. Each note area or 'tone field' on the handpan must resonate at a precise frequency, often necessitating numerous adjustments.</p>
<p>Many tuners now use electronic tuning devices to achieve greater accuracy. These devices can measure the frequency of the notes, enabling tuners to make precise adjustments. However, the final tuning often relies on the tuner's ear, blending technology with human intuition to create the perfect harmony.</p>
<p>Advanced tuners explore techniques like double-dome construction and air-gap tuning, which involve creating two domes with an air gap in between. This method enhances the richness and sustain of the notes, creating a more vibrant and dynamic sound.</p>
<h2>Heat Treatment and Tempering</h2>
<p>Heat treatment plays a crucial role in handpan manufacturing. This process involves heating the steel to specific temperatures and then cooling it rapidly. Heat treatment hardens the steel, making it more resilient and capable of holding its tuning longer.</p>
<p>Tempering, a controlled re-heating process, follows heat treatment to reduce brittleness and further enhance durability. The exact temperatures and methods used in these processes can vary between makers, often constituting part of their trade secrets and craftsmanship signature.</p>
<h2>Surface Finishing</h2>
<p>Once the handpan is tuned and treated, the next step involves surface finishing. This process not only enhances the instrument's aesthetics but also contributes to its longevity. Common finishes include sandblasting, painting, and applying protective coatings to prevent rust and wear.</p>
<p>Some makers also experiment with patinas and other artistic finishes, adding a unique visual appeal to their instruments. These finishes can range from simple, uniform coatings to intricate designs and patterns, making each handpan a work of art.</p>
<h2>Customization and Innovations</h2>
<p>Customization is a significant aspect of modern handpan manufacturing. Players often seek instruments tailored to their specific needs and playing styles. This demand has driven builders to innovate and experiment with different scales, sizes, and even the number of tone fields on the handpan.</p>
<p>Some recent innovations include the incorporation of electronic elements such as pickups and microphones, enabling amplified performances and recordings. These advancements expand the handpan's versatility, allowing it to integrate seamlessly with other musical technologies.</p>
<p>Another interesting development is the use of non-metal materials or composites for certain parts of the handpan. These materials can alter the acoustic properties in unique ways, offering new tonal possibilities and expanding the range of sounds a handpan can produce.</p>
<h2>Environmental Considerations</h2>
<p>With increasing awareness of environmental sustainability, many handpan manufacturers are adopting eco-friendly practices. This includes sourcing recycled metals, using non-toxic coatings and finishes, and minimizing waste in the production process.</p>
<p>Furthermore, some builders engage in initiatives that give back to the environment, such as planting trees or contributing to conservation efforts. These practices not only benefit the planet but also resonate with the handpan community's values of harmony and respect for nature.</p>
<h2>Conclusion</h2>
<p>Handpan manufacturing is a dynamic blend of tradition and innovation, art and science. From selecting the right materials to employing advanced tuning techniques and sustainable practices, every step plays a crucial role in shaping these captivating instruments. As the field continues to evolve, the handpan remains a testament to human creativity and the endless possibilities of sound sculpture, enchanting musicians and audiences worldwide.</p>
<div class="faq-section">
<h2>FAQs</h2>
<ul>
<li>
<strong>Q: What materials are commonly used in handpan manufacturing?</strong>
<p>A: The most common materials are nitrided steel and stainless steel. Some makers also experiment with hybrid materials or composites to achieve unique tonal qualities.</p>
</li>
<li>
<strong>Q: How is a handpan tuned?</strong>
<p>A: Tuning involves precise adjustments to each tone field's shape and tension to achieve specific frequencies. Advanced electronic tuning devices and the tuner's ear are used to ensure accuracy.</p>
</li>
<li>
<strong>Q: What is the role of heat treatment in handpan manufacturing?</strong>
<p>A: Heat treatment hardens the steel, making it more resilient and capable of holding its tuning. Tempering follows to reduce brittleness and enhance durability.</p>
</li>
<li>
<strong>Q: Can handpans be customized?</strong>
<p>A: Yes, handpans can be customized to fit specific scales, sizes, and player preferences. Additional innovations like electronic pickups can also be incorporated.</p>
</li>
<li>
<strong>Q: Are there eco-friendly practices in handpan manufacturing?</strong>
<p>A: Many manufacturers adopt sustainable practices, such as using recycled metals, non-toxic coatings, and minimizing waste. Some also engage in environmental initiatives like tree planting and conservation efforts.</p>
</li>
</ul>
</div>
</div>
</body>
</html>
Sound Sculpture: Innovative Techniques in Handpan Manufacturing
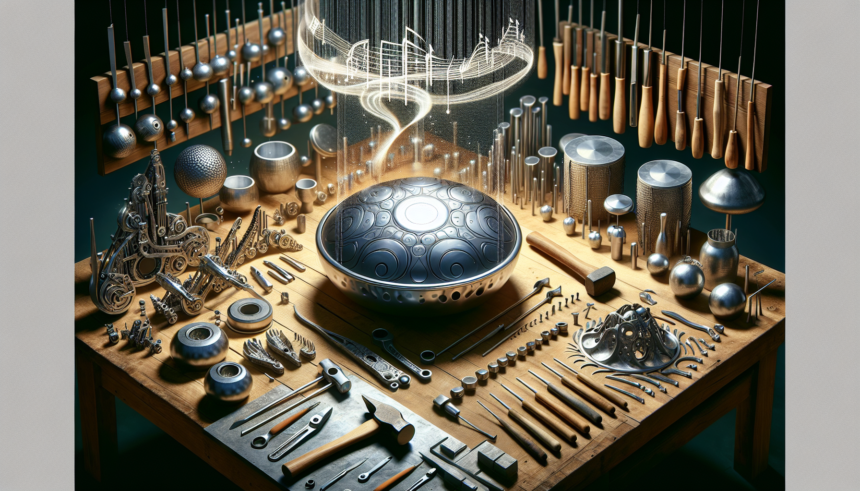
Leave a comment